Modeling & simulation
Optimize your designs from the start with our modeling expertise. Avoid costly iterations and refine dynamic behavior early on. Enhance product quality and cut development time, cost and resources by 50% or more.
Modeling objectives
The practice of modeling aims to optimize designs from the outset, avoiding expensive and time-consuming iterations. Particularly beneficial for refining dynamic behavior and assessing conditions impractical, costly, or risky to replicate in reality. Comprehend, refine, and rigorously test your designs early on.
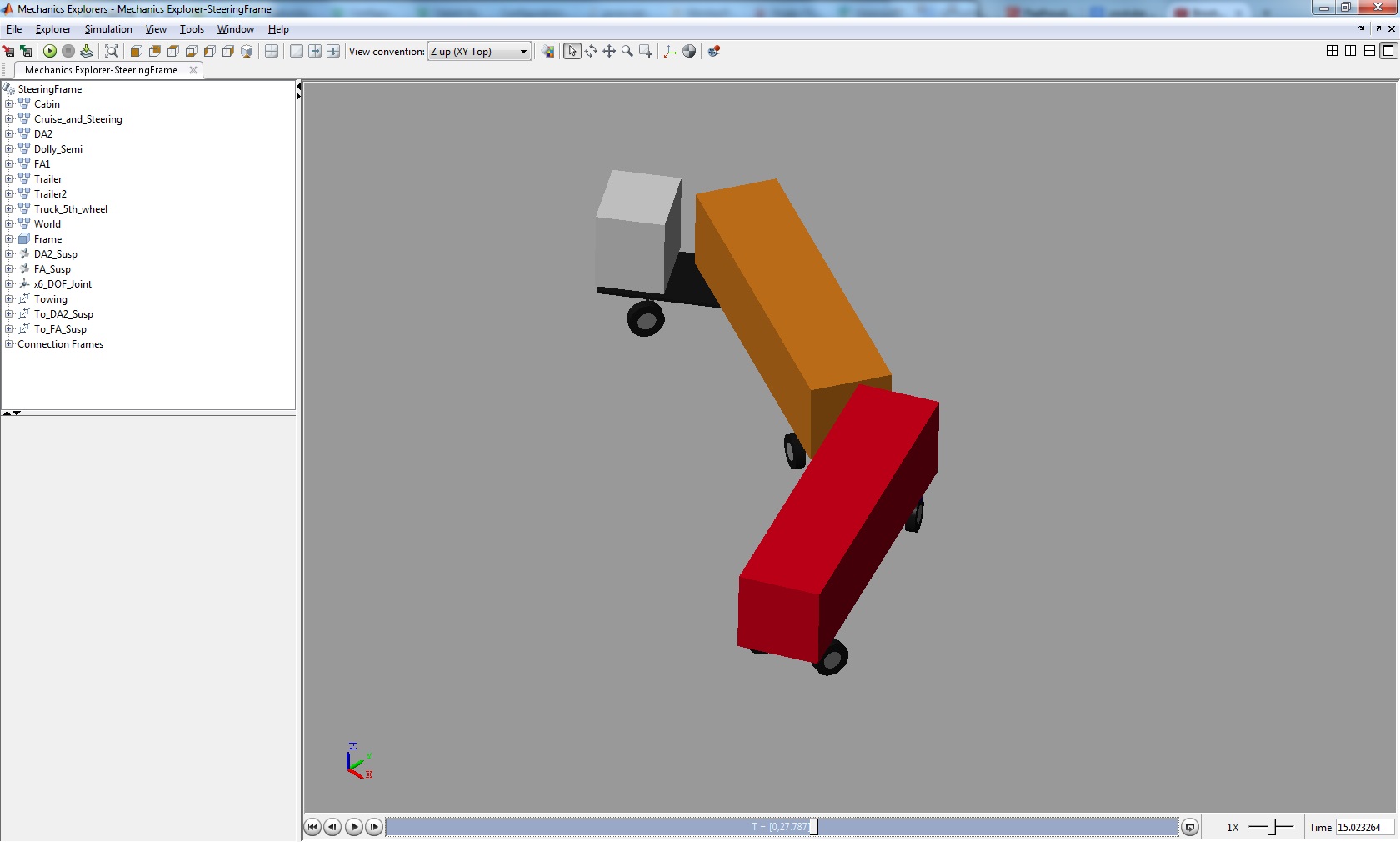
Understand dynamics
Explore dynamic system behavior with simulation at the required level of detail. Encompassing linear or non-linear dynamics, in any domain and application. Combine your simulation with control system models, to grasp and optimize system dynamics from the start.
Risk-free development
Numerous real-world experiments pose risks. Take new vehicle cruise-control algorithms, where discovering software flaws in simulation is preferable to on-road testing. Simulate impacts to gain insights into behavior under extreme conditions, minus real-world risks.
Saving time and money
Avoid waiting for time slots, procuring prototypes, and hardware iterations, saving both time and money. Mature your designs in simulation before entering the real world. And identify issues early, using simulation for rigorous system integration tests.
Visualization
Utilize animations and serious-gaming models for operator training, facilitating deep understanding and familiarity, prior to entering production. Observe dynamics that are difficult to capture without sensor capabilities, gaining even deeper insights into your system.
Failure mode effect analysis
What happens if sensors fail? What is the impact of system overloads? Is your system robust against emergency stops or power outages? Do fall-back strategies work? Perform dedicated FMEA analysis in simulation to methodically validate robustness.
Model-based control design
Engaging in control design? Model both your plant and your controller. Discover what works and what does not. Is your algorithm stable under all conditions? Are performance indicators met? And take the next leap: generate production code from your control model.
Simulation capabilities
Move your design process from the lab to your laptop: uncover system dynamics through mathematical modeling and simulation of diverse conditions and scenarios. Gain valuable insights and assume control of your development from the outset.
Embrace physical modeling where feasible and prototype your controls directly on your system for rapid and efficient development. Ensure software reliability through Hardware-in-the-Loop verification. Explore the potential of simulation with our expert guidance to accelerate your progress.
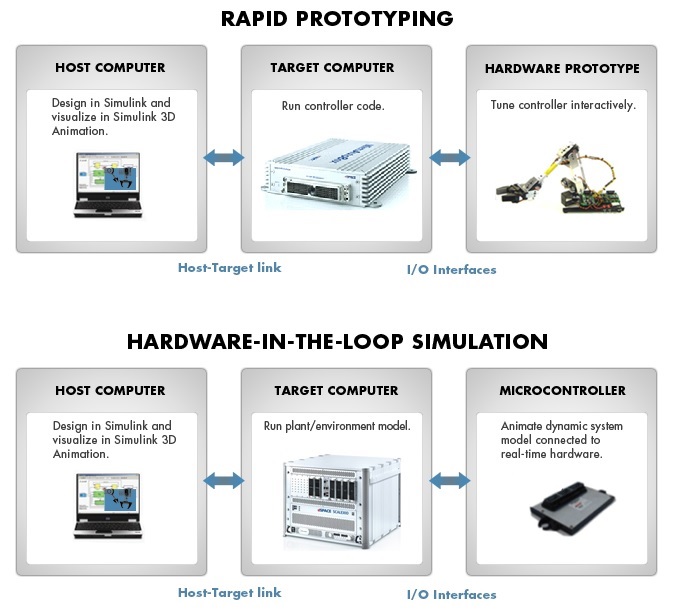
Physical modeling & advanced concepts
Leverage block systems to implement your mathematical model directly, or tap into SIMULINKs Physical Modeling libraries for domains such as mechanics, hydraulics, and electronics. Explore hybrid models that merge both paradigms. With proficiency in mathematical and physical modeling, we customize simulation platforms for peak performance.
For projects requiring innovative simulation concepts, we are poised to deliver excellence. As MathWorks partners, we collaborate closely with SIMULINK developers to unleash the full potential of your simulation environment.
Hardware interfacing
Models play a vital role in control design. Seamlessly integrate your simulation with hardware targets for control prototyping and embedded software testing. Two key simulation modes involving hardware are:
- Rapid Control Prototyping (RCP)
- Hardware in the Loop (HIL)
In RCP simulation, deploy your control system model on a prototyping target to validate and optimize strategies on real hardware, addressing performance and robustness challenges from the outset.
To validate production software, engage in HIL simulation to thoroughly test under various conditions, including simulated sensor failures and diverse success and failure scenarios.